Sheet metal process refers to the process of making up metal sheets in order to give them various parts and elements. Such components are applicable in various industries such as automotive, construction, electronic, and production. These processes involve cutting, bending, forming and joining. Awareness of this sheet metal fabrication process can save time and expenditures for businesses. It also assists during construction of higher quality products. This guide elaborates all the stages, tools involved, and the advantages of this process.
What is the Sheet Metal Process?
The sheet metal process is converting flat sheets of metal into a complete product. It’s achieved in several measures such as sheet cutting, forming and assembling. It may be a manual or fully automated process. Most modern factories rely on the use of machines to work at a fast pace and to be precise. Manufacturers typically use aluminum, steel, copper, and brass as materials.. These metals have strength and flexibility and hence the ideal ones in this work.
Why Is the Sheet Metal Process Important?
This process is widely used in almost every industry. It helps make parts like car bodies, airplane wings, and machine panels. Precision sheet metal fabrication ensures that every section cuts properly. And every part is fitting in place. The other advantage is that it allows building of prototypes. Using sheet metal prototype, companies have the ability to test designs prior to complete production. This saves time and eliminates the expensive mistakes.
Key Steps in the Sheet Metal Process
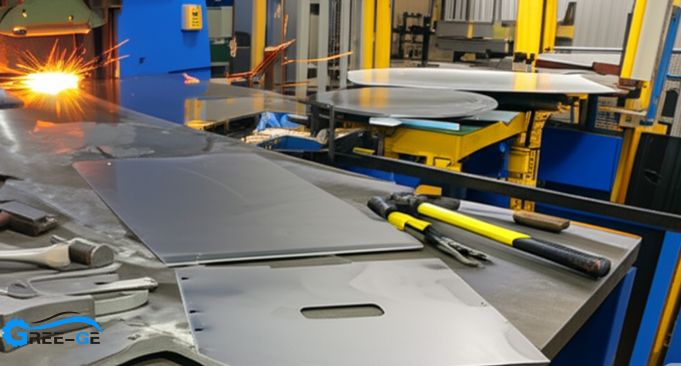
Each step plays a vital role. Below is a quick look at each phase of the sheet metal process:
Designing the Part
Designing is the first step. Engineers use CAD (Computer-Aided Design) software to draw 2D or 3D models. These drawings guide the next steps.
Sheet Cutting
In this step, large sheets are cut into smaller pieces. Tools used include laser cutters, shears, or CNC metal cutting machines. Accuracy is key here to avoid waste.
Bending and Forming
Now the flat sheets are bent into shapes. Machines like press brakes do this job. Bending adds angles and curves to match the design.
Joining or Welding
It depends on how strong the joint needs to be.
Surface Finishing
Finishing improves the look and protects the metal. It may involve painting, powder coating, or polishing.
Inspection and Quality Check
This ensures the product meets the required standards.
Tools Used in the Sheet Metal Process
Machines are vital in this process. They make the work faster and more precise. Below is a table showing some common tools and what they do:
Common Tools in Sheet Metal Process
Tool/Machine | Purpose |
Laser Cutter | High-precision sheet cutting |
CNC Punch Press | Punching holes and shapes |
Press Brake | Bending metal sheets |
Welding Machine | Joining parts together |
Deburring Tool | Smoothing rough edges |
Shearing Machine | Cutting large sheets |
CAD Software | Designing parts and models |
Materials Used in Sheet Metal Process
Each metal has its own strength and use. Below is a list of commonly used materials:
Common Materials in Sheet Metal Fabrication
Material | Features | Common Use |
Aluminum | Lightweight, corrosion-resistant | Aircraft, auto bodies |
Stainless Steel | Strong and shiny | Kitchen tools, medical equipment |
Mild Steel | Cheap and easy to shape | Construction, machinery |
Copper | Good electrical conductor | Electrical parts |
Brass | Corrosion-resistant, golden color | Decorative parts, valves |
Benefits of Precision Sheet Metal Fabrication
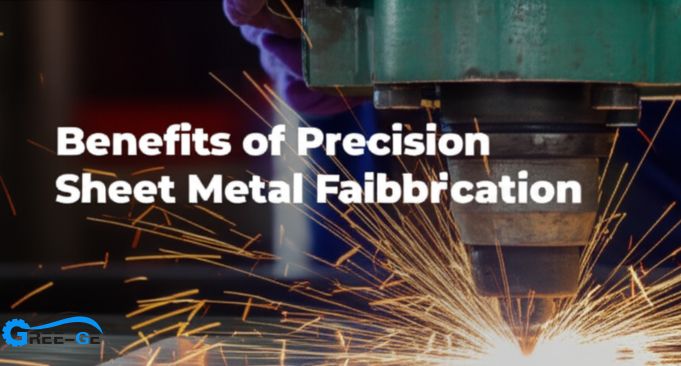
Using precision sheet metal fabrication means better quality and less waste. Machines used today are very accurate. They cut and bend within a margin of millimeters. This ensures all parts fit well, especially for tight spaces. It also speeds up production. What used to take days can now be done in hours. CNC machines can run non-stop, which increases output. This is useful in large orders or when time is short.
Importance of Sheet Metal Prototype
Before full production, engineers often create a sheet metal prototype. This sample product is made using the same steps. It helps check if the design works well. Engineers can find and fix problems early. Making a prototype costs less than producing a full batch. It’s a smart move that saves money and avoids delays later.
Sheet Metal Fabrication vs Traditional Methods
Old methods used hand tools and were slow. Today, sheet metal fabrication is more advanced. Machines like CNC metal cutting machines do the job faster and better. They execute digital instructions and hence each cut and bend is precise. However, modern sheet metal tools are best suited in big projects.
Tips for a Successful Sheet Metal Process
Here are a few tips to make your project a success:
- Always start with a proper design.
- Choose the right metal for the job.
- Use advanced machines for better results.
- Create a sheet metal prototype first.
- Double-check measurements before cutting.
These tips help reduce errors and improve the final product.
Industries That Use Sheet Metal Process
This process is used in many fields. Some examples include:
- Automotive: Making car bodies and engine parts.
- Aerospace: Building airplane wings and cabins.
- Construction: Creating metal roofs and wall panels.
- Electronics: Making cases for gadgets and machines.
- Medical: Fabricating surgical tools and equipment.
Each industry has its own standards, so the process may change slightly to meet those needs.
Final Thoughts
Sheet metal process is a reliable and quick method of manufacturing metal parts. You obtain accuracy by using such tools as CNC metal cutting machines and software. With sheet cutting, forming, and welding you can create custom but strong parts out of flat sheets. It is very affordable, efficient, and suitable to most industries. When you are planning a project, note that you should build a sheet metal prototype. It is time-saving and it prevents errors. Precision sheet metal fabrication will help you achieve the high quality at a shorter period of time.
FAQs
What is the sheet metal process used for?
People use it to make metal parts for cars, planes, buildings, and machines.
What machines are used in sheet metal fabrication?
Laser cutters, press brakes, CNC machines, and welding tools are common.
What is the benefit of a sheet metal prototype?
It contributes in testing and enhancing designs before full production.
What are the best materials in the fabrication of sheet metals?
The common materials are aluminum, steel, copper and brass.
How accurate is modern sheet metal fabrication?
With CNC machines, accuracy can be within millimeters.